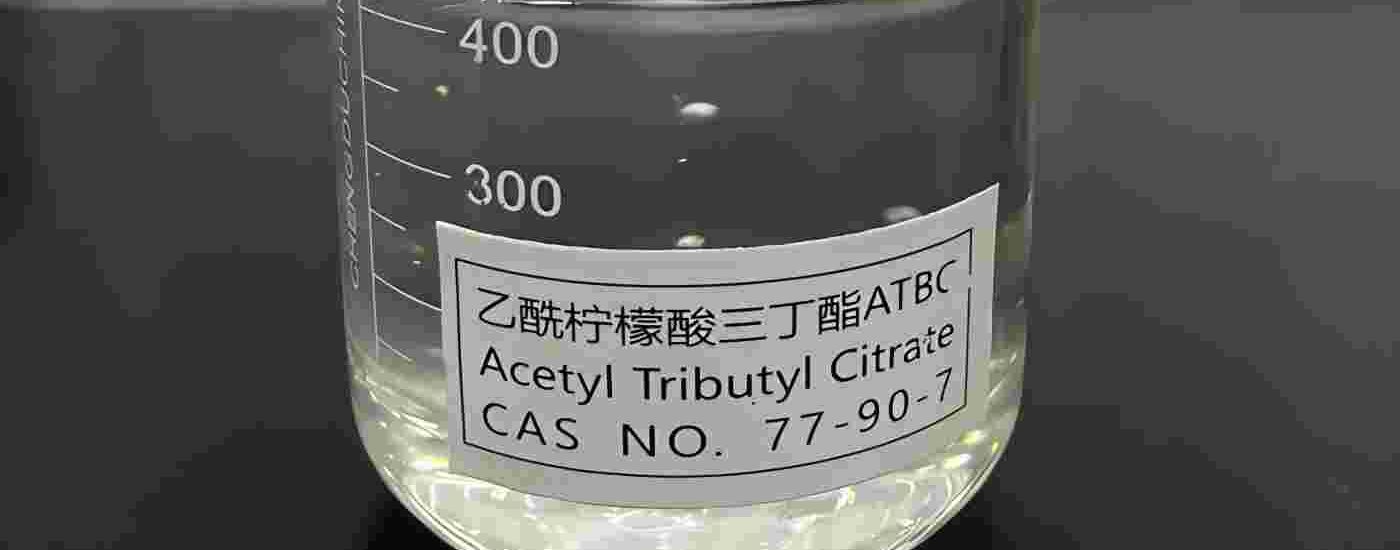
Performance characteristics
Excellent plasticizing performance: ATBC (acetyl tributyl citrate), as a plasticizer, can effectively reduce the force between polymer molecular chains. It is inserted between the molecular chains of polymers (such as polyvinyl chloride (PVC)) to increase the distance between molecular chains and make the movement of polymer chains easier, thereby significantly reducing the glass transition temperature (Tg) of the polymer. For example, in PVC processing, adding an appropriate amount of ATBC can transform the PVC material from a hard and brittle state to a soft and elastic state, and this plasticizing effect has good durability. Compared with traditional plasticizers, ATBC has higher plasticizing efficiency for polymers. It can achieve a softening effect comparable to other plasticizers at a lower addition amount, which not only reduces costs, but also reduces the residual amount of plasticizers in the polymer and improves product quality.
High safety: ATBC is a non-toxic or low-toxic plasticizer. It has undergone rigorous toxicological tests, such as acute toxicity test, chronic toxicity test, teratogenicity test, etc., and the results show that it poses minimal harm to human health and the environment. This is because its chemical structure is relatively stable and does not produce harmful metabolites in the human body like some toxic plasticizers.
Due to its high safety, ATBC has become one of the preferred plasticizers in many fields with stringent hygiene and safety requirements, such as food packaging, medical devices, etc.
Excellent compatibility: ATBC has good compatibility with a variety of polymer materials. In addition to having good mixing properties with PVC, it can also be evenly blended with various plastic materials such as polyester, polyurethane, and acrylic resin. In polymer systems, it can be dispersed at the molecular level without delamination or precipitation. For example, when manufacturing multi-layer co-extruded plastic films, ATBC can ensure good adhesion and compatibility between different layers.
Good chemical stability: It has good acid, alkali and salt resistance. ATBC can maintain its chemical structure relatively stable under different chemical environments. For example, in some plastic products that may be exposed to weakly acidic or weakly alkaline substances, such as food packaging containers, medical consumables, etc., ATBC will not decompose or degrade due to corrosion by chemical substances.
Strong migration resistance: It has good migration resistance in polymer systems. ATBC does not migrate easily from the polymer when in contact with other materials or under different environmental conditions. For example, in food packaging materials, it will not migrate into the food, ensuring food safety; in multi-layer composite materials, it will not migrate between different layers, thus maintaining the performance of the material.
Biodegradability: ATBC has certain biodegradability. Under appropriate environmental conditions, such as composting or the action of specific microorganisms, it can gradually decompose and reduce long-term pollution to the environment. This feature makes it more advantageous in today’s increasingly environmentally conscious environment.
Application areas
Food packaging field: ATBC is widely used as a plasticizer in food packaging materials, such as PVC food packaging films, plastic containers, etc. It can make packaging materials have good flexibility, transparency and water resistance, while ensuring that packaging materials meet food safety standards and will not migrate harmful substances into food, ensuring food safety and quality.
Medical device industry: ATBC plays an important role in medical plastic products, such as medical catheters, infusion bags, blood bags, medical gloves, etc. It can make these medical devices have appropriate softness and elasticity, making them easy for medical staff to operate, while ensuring the safety of patients and not causing adverse physiological reactions to the human body.
Children’s Toy Manufacturing: Since children may chew toys, the safety of toy materials is critical. ATBC is used as a plasticizer in toy manufacturing to make toys soft and comfortable to the touch and comply with strict toy safety standards without causing harm to children’s health. Poisoning, etc.
In the field of building materials, in some building plastic products, such as PVC pipes, door and window profiles, etc., ATBC can improve the processing performance and physical properties of the materials. It can make the pipe more flexible and easy to install, while improving the weather resistance and durability of door and window profiles and extending the service life of building materials.
Application method
Direct addition method: During polymer processing, adding ATBC directly to polymer resin is the most common application method. For example, in PVC processing, ATBC and PVC resin are fully mixed in a high-speed mixer according to a certain formula ratio (usually the amount of ATBC added is about 10% – 50% according to the required softness and other properties of the product). The mixing temperature is generally around 80-120°C and the time is about 10-30 minutes to make ATBC evenly dispersed in the PVC resin, and then made into plastic products through extrusion, injection molding or calendering.
Blending method: ATBC can be blended with other plasticizers or additives. In some cases, in order to achieve better performance effects, such as improving flexibility and cold resistance at the same time, ATBC will be mixed with other plasticizers (such as epoxidized soybean oil) in a certain ratio (such as ATBC: epoxidized soybean oil = 3 :1 – 5:1) before adding to the polymer after blending. This blending method can comprehensively utilize the advantages of different plasticizers to optimize the performance of plastic products.
Multi-layer composite applications In the manufacture of multi-layer composite materials, ATBC can be used in different layers of plastic materials. For example, when manufacturing food packaging materials with barrier properties, the inner layer can be PVC with ATBC added to provide flexibility and compatibility with food; the outer layer can be a material with barrier properties, such as polyterephthalene. Ethylene glycol formate (PET). ATBC can help better bonding between different layers in this multi-layer structure, while exerting its plasticizing effect in each layer to improve the performance of the entire composite material.